Situation
In the wake of significant growth, Malco Products found themselves running short of manufacturing capacity in 2016. The tool manufacturer needed more space, equipment and skilled labor to keep up with demand for products they had recently innovated. Collaborating with University of Wisconsin-Stout Manufacturing Outreach Center (MOC), the company once again applied innovative thinking to meet this challenge.
Solution
Familiar with Innovation Management System (IMS) through previous work with UW-Stout MOC, Malco Products seized the paradigm shift this system brings. Originally the company entertained ideas of expanding the existing facility or building a new one. Taking an innovative approach, they opened their minds to the possibility of utilizing an older building outside their local area, and in early 2017 purchased a 346,000 square foot plant located in DeWitt, Nebraska.
Closed since 2008, the former Vice-Grip plant will soon re-open as Malco Product's manufacturing site for the multi-tier Eagle Grip locking pliers. The new product line will make a domestically produced locking pliers a reality again for the first time in nearly 10 years, while providing opportunity for DeWitt's skilled workforce.
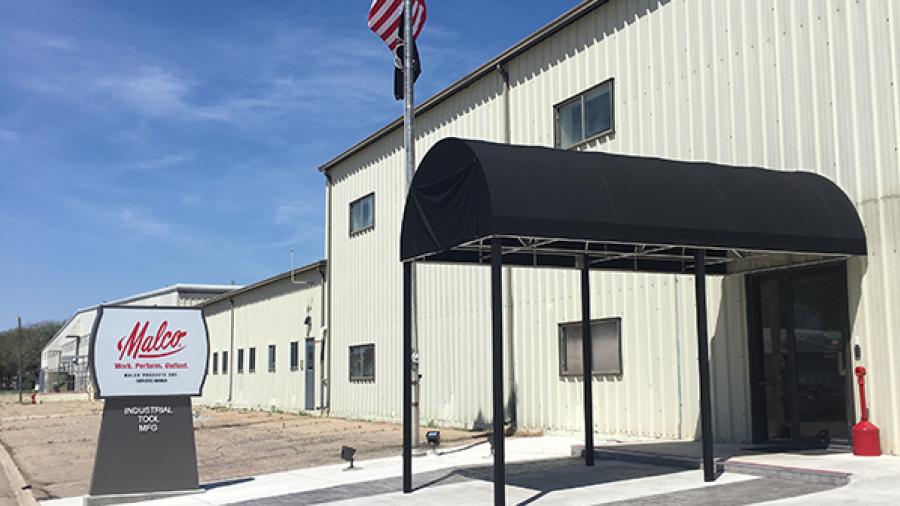
Results
Manufacturing is scheduled to begin at the DeWitt site in fall 2018 and Malco looks forward to introducing new Eagle Grip products in 2019. "We attribute this success, in large part, to innovative thinking initiated here by UW-Stout MOC," said Eric Peterson, Malco Products Director of Sales and Marketing.
According to Peterson, Malco Product's new approach has already helped the company grow and avoid significant costs, including:
- $50M in cost avoidance by expanding to existing facility rather than building new
- $4.2M in cost avoidance by utilizing older, refurbished equipment
Peterson anticipates future benefits from:
- Revenue from new Made-In-America Eagle Grip products
- Hiring savings resulting from the DeWitt skilled workforce and available resources
- Increased brand awareness and sales due to reshoring comeback story