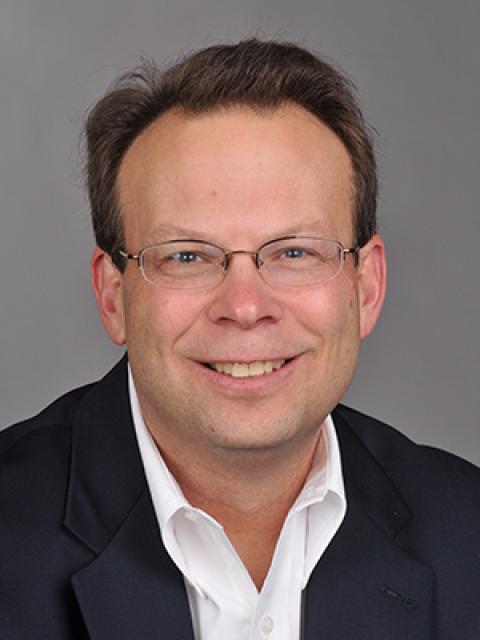
Reprinted with permission of the Eau Claire Leader-Telegram
(Published April 7, 2020, Page 3A)
By Ryan Patterson
Eau Claire Leader-Telegram
Personal protective equipment like ventilators and masks are in short supply in some parts of the county facing COVID-19. The lack of equipment is due to many reasons, but the basic reason is demand for the materials far exceeded supply and companies are unable to quickly respond to the increased demand.
That is where supply chain management comes in. The area deals with “the flow of materials and the flow of information from the lowest-level supplier to the end consumer,” according to Gene Gutman, UW-Stout associate professor of supply chain management and director of the supply chain management undergraduate program.
Gutman recently spoke with the Leader-Telegram about supply challenges, how the coronavirus might impact companies’ future decisions and a metaphor to think about surge capacity.
The interview has been edited and condensed.
It seems like COVID-19 has affected most supply chains to some degree, is that fair to say?
It’s causing disruption … and the reason for this is we have such a tremendous surge in demand that’s unprecedented. Typically, the way supply chains work is supply chains plan for somewhat normal or constant demand, and then they plan for variation. There’s typically variation on a day-to-day or a week-to-week or a month-to-month basis in terms of what people consume, and that variation isn’t anywhere near what we’re seeing today in terms of certain products. What happens is this ripples all the way back to the suppliers who supply raw materials, components, sub-assemblies, and then to the manufacturers who actually do the fabrication and final assembly of the product.
Is there a certain industry or product that’s been most impacted?
It’s clear the medical supplies are seeing the surge in demand. We saw something as simple as toilet paper as a surge in demand. If you think about toilet paper being normal demand, that’s probably about as constant as it gets. People use the same amount every day, and when all of a sudden they go and buy large amounts of toilet paper you have a surge. Companies just aren’t able to scale the business to be able to deal with this … When things are going well, people don’t even know about the supply chain. You expect milk, bread and toilet paper to show up every day at the grocery store. You just don’t think about it.
Is there any similar precedent, anything remotely to compare this to?
Ironically, yes. It depends how you look at the question … When we had Hurricane Katrina (in 2005), that created a huge, huge surge in demand in that region for different items and supplies. Or you go back a few years (to 2011) when there was the tsunami in Japan … We’ve seen it many times from a pure supply chain perspective. Where we haven’t seen it is the broad-scale economic and social impact this is causing, where so many businesses are severely impacted across the country and across the globe. When Hurricane Katrina hits or a tsunami hits, it’s somewhat localized to that region. This is hitting the economy and people’s everyday interaction and social activity on a global scale, and we have not seen that before.
Is there a most concerning aspect from a supply chain perspective?
What’s most concerning is that we do not know how long and how deep this is going to last. How bad is this going to be? The unfortunate thing is people are dying, and the economy is being hit severely … The other concern is that if the front line in the supply chain gets decimated, that can really, really, really be troublesome. And when I say the front line, it can be the health care workers … trucking and warehouse people to deliver food to grocery stores, people who manage power plants.
Anecdotally, what have supply chain people learned from this situation over the past month?
Unfortunately, this is a great way to teach supply chain concepts. When we talk about surge in demand, we can illustrate what’s going on with medical supplies. We can talk about stockpiles, and when we talk about lead time or time it takes to replenish, we have real-life examples that we can use as teachable concepts.
When the country gets out of the worst of this, how do think companies will change their supply chain management, if at all?
Companies are constantly evaluating and re-evaluating their supply chains, so I don’t believe there will be one magic way to do this … I think companies will continue to make conscious decisions on where to source products … They’re constantly balancing risk, they’re balancing costs, they’re balancing the ability to respond and scale, they’re balancing quality, they’re balancing lead time and they balance how to protect their intellectual property. These factors drive if they source locally, regionally, domestically or globally.
One of the things I use as an example to illustrate “surge capability and how can people understand it?” The example I use is most people in their life have baked a cake or have made cookies. Most people have ingredients at home to bake a cake or make cookies, and all of a sudden there’s a bake sale going on and you’ve been asked to make some cookies or make a cake, and you decide, “OK I’m going to make a couple cakes for the bake sale or a couple dozen cookies,” and you may have to go to the store. There’s plenty of those ingredients on the shelf, and you come home and you make your cakes and away you go.
All of a sudden the bake sale calls up and says, “You know what? I need 10 cakes or 10 dozen cookies.” And you say, “I think I can still do that, but I’m going to have to work really hard to do that,” and you go back to the store and get more ingredients. Then while you’re out, they call you up and say, “You know what? We need 100 cakes.” There’s no way you can physically make 100 cakes for tomorrow with one oven, so what do you do? You call your friends, you say, “Can each of you make 10 cakes?” Then the 13-time World Champion Green Bay Packers call up and say, “We want to have a cake or a cookie for everybody who’s coming to the game on Sunday, and we want that cake or cookie to be in the form of the Lombardi Trophy or the Packer logo.”
So, you need to make 80,000 cakes by tomorrow, and you don’t even have cookie cutters or a cake mold to do this. We now have to buy cookie cutters or cake molds to do this, and there’s no way the grocery store’s going to have enough ingredients to make 80,000 cakes. So, then what happens is the rest of the world is getting wind of this, all of the countries around the world call you up and say, “Guess what? We want a cake for every single person on the planet. Eight billion cakes.” This has all happened in a matter of a couple days. Well guess what? There aren’t enough eggs on the planet to make eight billion cakes, so what do you do? We need more chickens to lay eggs, so we need to breed chickens, the chickens need to lay eggs, we need to hatch the eggs, we need to grow chickens to become adults. All of this will take a few months before chickens can even start producing eggs. Then, we need to package and distribute the eggs to the grocery store. While all of this is going on, the health department hears about our bake sale and they want to come in and certify our facility. We will need to apply for a license.
This simple example illustrates how this concept of surge capacity works — people and businesses can only grow and surge so much before they hit their capacity limit. Companies have no more capacity, because they are running 24 hours a day, seven days a week, every single piece of equipment they have. We can’t bake more cakes if we don’t have any more ovens. We can’t bake more cakes unless we have more ingredients. It’s physically impossible …The challenge is you would not keep all of these ingredients on hand; they have a shelf life and spoil, and you would not have all of the extra ovens sitting idle for something that happens so infrequently. It is not a piece of cake!
Supply chain people deal with this every day and know how to address these issues. The issue isn’t knowing what to do. The issue is being able to do it and having the capability to do it.
###
Photo
Gene Gutman