At C&N Manufacturing in central Wisconsin, the daily arrival of a FedEx semi driver to take away packaged orders should have been a good sign – products were in the pipeline. Business was good.
To the trained manufacturing eye, however, there was a problem. The Boyd company, which makes storage trunks and products for thousands of children attending summer camps and for outdoors enthusiasts as well, was making the FedEx driver wait. And wait.
The Everything Summer Camp orders that were supposed to be ready to ship by the end of the day often were not ready, especially during the busy season in the spring. The problem wasn’t just packaging and shipping — it went up the line, all the way to the production floor.
“We couldn’t handle any more sales. That was a real wakeup call,” said C&N Vice President Mark Sieglaff.
When President Ed Holand and Sieglaff realized their system had flaws, Holand contacted the Manufacturing Outreach Center at University of Wisconsin-Stout, which specializes in helping small manufacturers improve their operations by becoming more efficient, productive and, ultimately, profitable.
“They wanted to make improvements, serve their customers and meet demands better but weren’t quite sure where to start and what to address,” said Ted Theyerl, SMOC senior management engineer.
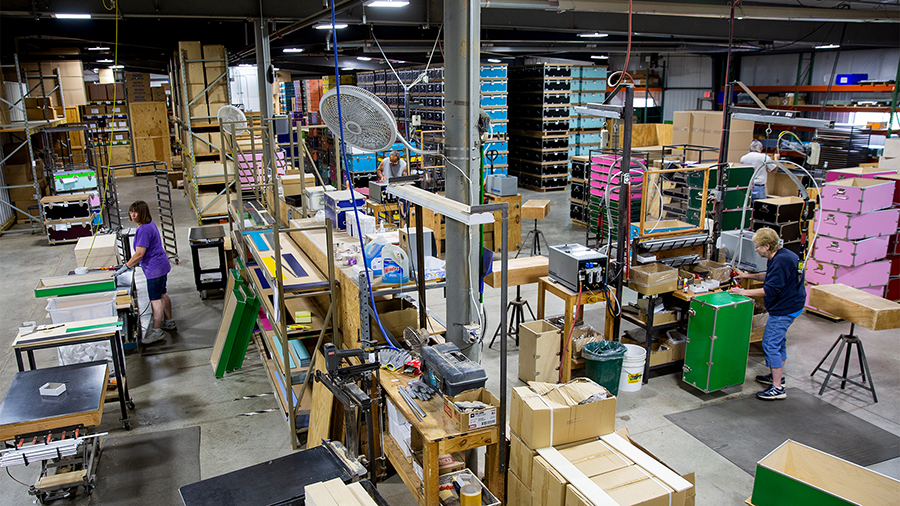
Lean training changed everything
The road to a more efficient C&N Manufacturing began when Theyerl and SMOC Project Manager Aaron Bialzik arrived at C&N with a box of Legos, the colorful kids’ building blocks. The MOC uses Legos for a manufacturing simulation activity to help clients visualize potential changes to the production process. C&N employees began to see the possibilities.
Lean training, which identifies and eliminates various types of waste in the manufacturing process, began with C&N’s trunk-makers.
“When we first visited, I’d see stacks of 50 trunks unfinished between processes. One production area would get away ahead of another. After the training and process evaluation together, employees made some significant changes to the layout and process to improve flow,” Theyerl said.
One of the keys was creating a tighter production space. Workers were too far apart from each other to realize when one area got ahead of another. They moved closer together, balanced the processes and were cross-trained. “In one week, the production employees made changes to the layout of the production floor to balance the process times, limit work in process, improve the flow and agreed to help each other out,” Theyerl said.
The result: Large batches of partially finished trunks no longer piled up. A steady flow of finished trunks began to come off the line at a predictable daily rate.
One of the eight wastes in Lean manufacturing is waiting. Sieglaff remembers the FedEx driver having to wait for up to 30 orders to be labeled before shipping. After the Lean changes, the driver no longer had to wait. “The driver asked, ‘What are you doing different from last year?’” Sieglaff said.
Improvements down the line
The improvements went so well in production that Theyerl and Bialzik did the Lego simulation and Lean presentation next in graphic design, then shipping and then for office personnel. Legos and Lean had a domino effect.
Even the customer service area benefited: An improved production process resulted in fewer mistakes being made and more satisfied customers. Less phone time for them also equaled more time to assist production, if needed.
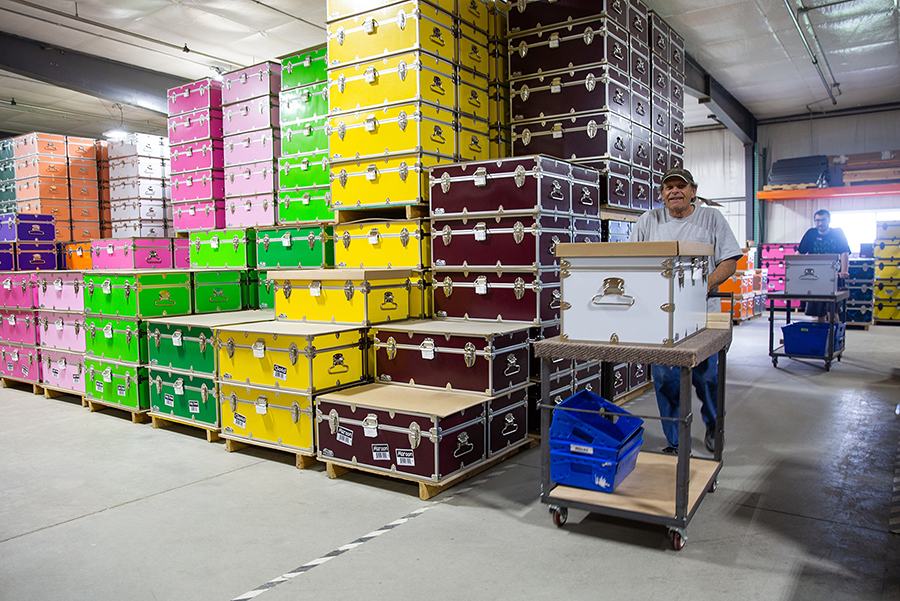
Previously during the C&N busy season, some orders had to be turned down because the staff didn’t know if they could be filled in time.
“We’re now getting a consistent flow each day, so that allows us to get ahead of the sales curve,” Sieglaff said. “Now, we can project what will ship for a day based on the hour of the day. It’s engineering the line to the pace of customer demand.
“If we had gotten a big contract before and had to double production, there was no way we could have done it. Now, we know exactly what it would take to increase production 25% or 200%.”
Changing company culture
Sieglaff said many employees at first were skeptical of Lean and reluctant to change the way they had always done things.
“They would come out of the Legos presentation and say this was the better way but it wouldn’t apply to their area or process. They said, ‘I suppose we could try processing six or 10 orders at a time.’ As they got into it, it was great to watch people come to their own conclusions,” he said.
As they started to embrace, test and implement changes, they began to work toward processing one order at a time.
Sieglaff had a long list of Lean changes he wanted implemented, but he soon realized he couldn’t force the changes. “It came down to letting employees know it’s OK to try new things,” he said.
Theyerl agrees. “The key to their success is that management believed in the Lean manufacturing philosophy and supported letting all employees experiment with ideas. There is no magic wand for improving. Everyone has to be involved, management through production. Everyone in the company needs to be headed in the same direction and understand what waste is.”
The changes started in 2018 and are continuing, Sieglaff said. Everyone on staff, about 25 full time and 45 total during the busy season, has bought into the new approach. With a more unified staff, communication also has improved.
“From 2018 to now, you don’t see people stressed out and running around and product piling up. Everything is at a nice pace,” said Sieglaff, remembering the days when people worked overtime and still fell behind.
“There’s definitely a change in culture — less control from management and more control for employees to improve their processes,” he said.
C&N poised for more growth
C&N, started in 1987 by Craig and Nancy Cornell, has been in its current production facility in Boyd since 2003.
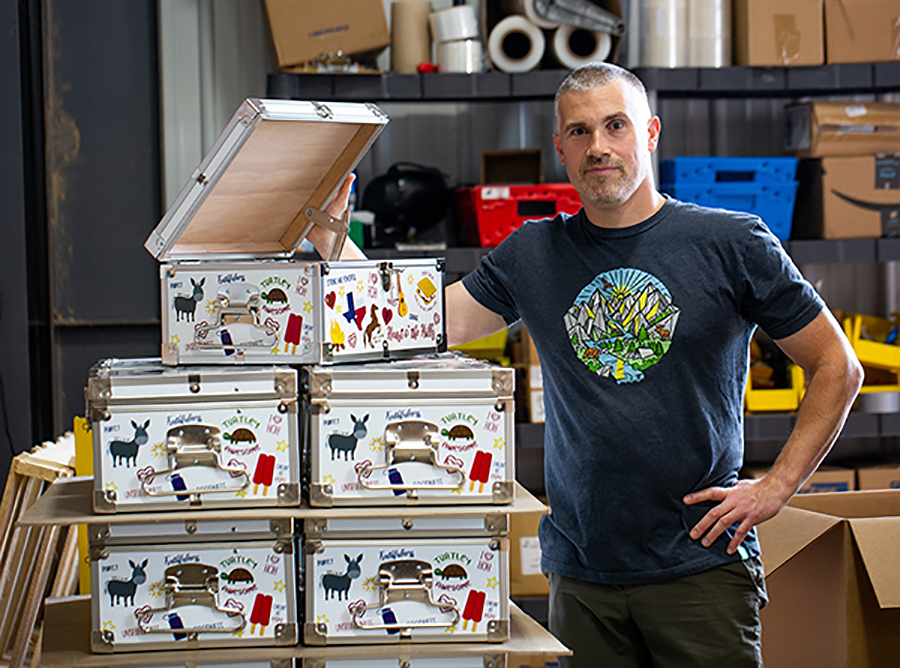
Customers can buy from a catalog, but most of them find C&N’s products on the EverythingSummerCamp.com website.
C&N also began selling on Amazon two years ago, opening new market areas. That caused a spike in sales and led to the need for changes.
Prior to the COVID-19 pandemic, the company was on track to have its best year ever. Despite most summer camps being closed in 2020, C&N is receiving orders but hasn’t been able to secure staff like normal. “Thanks to the MOC and the flexibility that comes with being lean, C&N has been able to shift employees into new roles to meet customer demand and keep the company moving forward toward a brighter 2021 camp season,” Sieglaff said.
“We’re really starting to blur the lines between departments. Everybody is working together. Lack of stress, knowing what tomorrow will look like, and having employees be responsible for what their workday will look like has made a huge difference,” Sieglaff said.
That makes Theyerl happy. “We pretty much worked ourselves out of a job. C&N understands it, can do it and own it, and that’s ideally what we like to do and see happen in a successful project,” he said.
The Manufacturing Outreach Center is part of UW-Stout’s Discovery Center, the university’s primary outreach and engagement organization.
###
Photos (top to bottom)
A FedEx semi sits at the loading dock recently at C&N Manufacturing in Boyd.
C&N employees work on trunks in the production area.
Lois Lingen attaches hardware on a trunk.
Jim Armbrust attaches hardware on a trunk.
Bob Bellick, left, and John Sieglaff pick up trunks to prep for shipping.
John Sieglaff picks a rain jacket to fill a C&N order.
Deb Techmeier cuts custom fabric to make a designer laundry bag for a summer camper. She sewed the bag at another production station.
Mark Sieglaff, C&N vice president, inspects an order of custom minitrunks for Heart O’ the Hills Camp in Hunt, Texas.
Ted Theyerl, UW-Stout Manufacturing Outreach Center senior management engineer