At the L.E. Phillips Career Development Center near downtown Eau Claire, about 275 employees make dozens of products and provide services in 10 departments.
Thanks to a project with School of Engineering students at University of Wisconsin-Stout, the center’s woodworking department soon will have a better way to make one of those products — box frames for queen-size beds.
Over the past 18 months, three groups of UW-Stout students have designed, built and automated a system that will be safer for employees and could help CDC produce about twice as many box frames a day.
Recently, four seniors wrapped up work on the automation aspect of the $40,000 CDC-funded project. When another team finishes testing and optimizing the control system in the fall, it should be ready for delivery.
“The students have done a great job. It’s going to work out just perfectly,” said Gregg Mizerk, CEO of the Career Development Center, which employs and serves people needing to learn a job skill, are facing disadvantages or have disabilities.
“It feels great knowing we are doing something that’s going to impact people’s lives and help folks who are disadvantaged,” said Alex Kowalczyk, of Mondovi, a manufacturing engineering major.
With the current system in Eau Claire, CDC employees nail one side of the box frame with hand-held nail guns, then two people flip it and nail the other side — a total of 224 nails. It takes about 15 minutes.
With the automated system, two pneumatic nail guns — for two sizes of nails — ride on a gantry over the frame. One side of the frame, or 112 nails, is nailed in about a minute.
The frame then is ejected from the aluminum stand designed and built by students, a plexiglass safety door opens and one employee, instead of two, can slide it off to nail the other side. The new process will take from five to seven minutes, or less than half the time.
If the CDC were to buy a similar system on the market, it would cost four to five times as much, up to $200,000, said Assistant Professor Danny Bee, an adviser on the project along with colleagues Glenn Bushendorf and Paul Craig.
To automate nailing on both sides of the frame, an even more costly system would have to be developed.
“The payback will be less than a year,” Mizerk said. “We’ll be able to almost double the capacity. We have vendors with larger demands, so we’re looking at making that happen with those vendors. We can use the proceeds to reinvest in training and programs for the people we serve.”
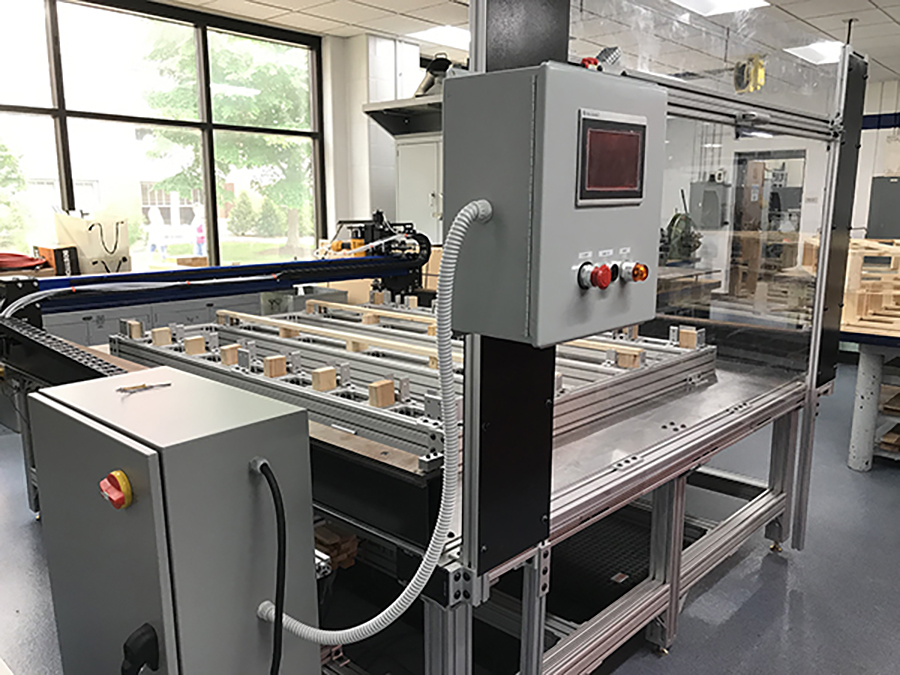
About 75 percent of CDC revenue comes from manufacturing, he said.
The Career Development Center also could reprogram the system to make another one of its products, twin-size box frames. UW-Stout students are providing operating manuals with the system.
Everyone benefits
The greatly reduced time using nail guns by hand will improve safety for CDC workers, Mizerk said.
Also, CDC employees using the new system will gain experience with automation. “We’re looking to enhance the skills of the people we employ so they can earn more and find a job in the community,” Mizerk said. “We want to build confidence in people.”
Students have gained valuable real-client experience working on the project, said Zach Dahl, of Buffalo, Minn., a mechanical engineering major. “We learned a lot with the technology aspects of the project, and having our name on it was a big thing,” he said.
For the spring semester alone, students estimated that they put about 800 hours of research and labor into the project, including some 10-hour days. Two members of the team spent their spring break working on it in Fryklund Hall.
“You can solve a problem if you put your time and effort into it,” said Jordan Roessler, of Tomahawk, mechanical engineering.
Reid Zaborowski, of Hager City, mechanical engineering, said he enjoyed the team and project leadership aspects and appreciated the support of professors. Learning some electrical engineering was a bonus, he said.
All four team members graduated in May.
Mizerk visited the students at the end of the spring semester to review their progress. Students toured the CDC at the start of the semester. “They put a lot of time in it, and you can see the passion they have for working with the equipment. It’s a pleasure working with them,” Mizerk said.
Students have overcome a variety of engineering challenges. “With the setbacks they had, they came a long way,” Bee said.
Projects like this one are why UW-Stout engineering graduates “hit the ground running. Their opportunities to apply what they’ve learned in class is a strength of our programs,” Bee said.
Engineering students, with faculty supervision, regularly work with business and industry, such as Hormel and Curt Manufacturing, to help solve problems while gaining practical experience. For more information, contact Bee, beed@uwstout.edu.
###
Photos
Gregg Mizerk
Danny Bee
The box frame automation system includes a table for the frame, computer interface controls and a plexiglass door, where the box frame is pulled off.
A finished box frame with the automation system in the background.